Services
Testing & Analysis
The root cause of reliability problems is often elusive. Getting to the root cause requires more than one test or another. It requires a history grounded in careful, clever investigation.
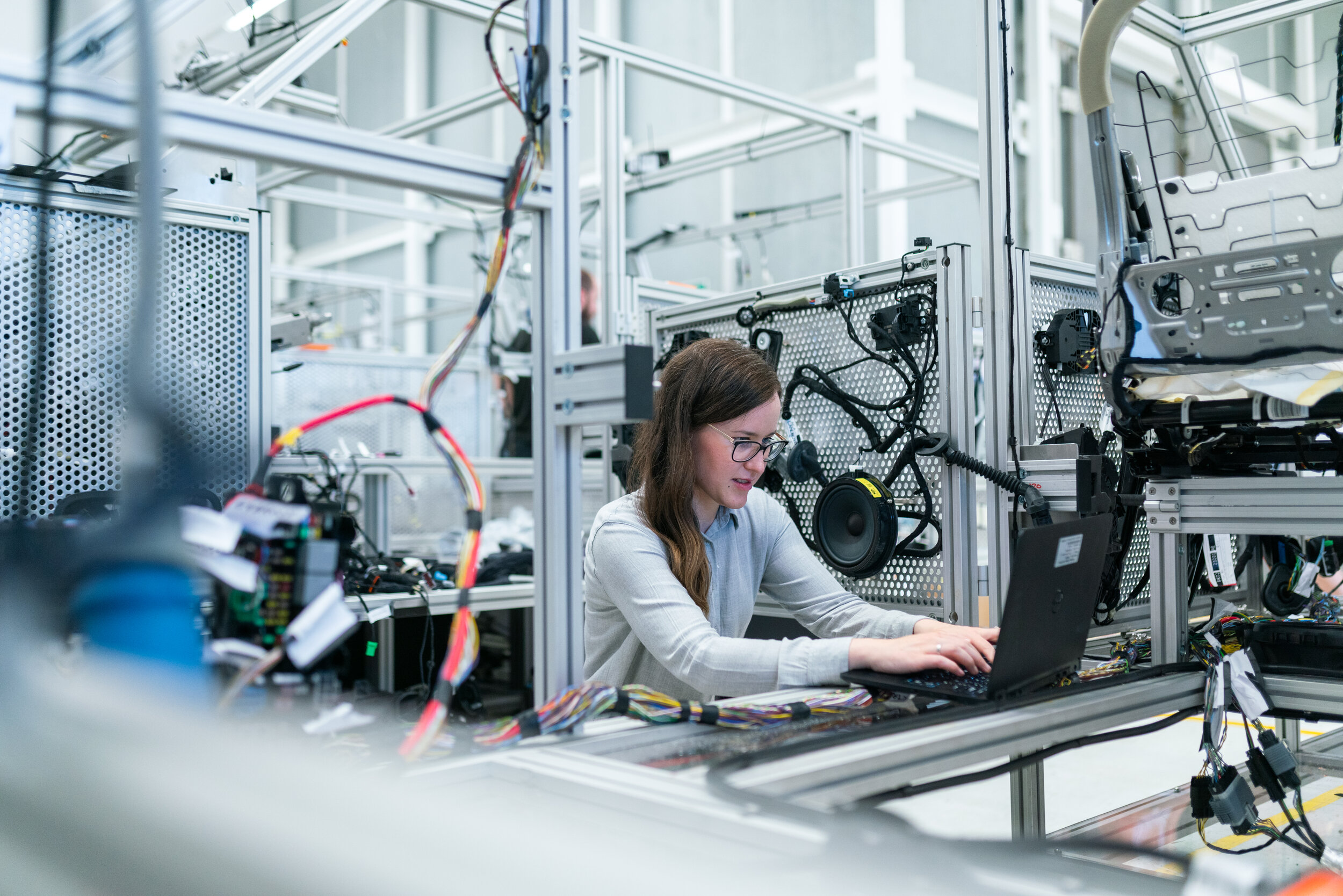
Testing & Analysis Services
Ion Chromatography for Electronic Assemblies and Bare Boards →
Tests for contaminants that often contribute to electrochemical failures.
Environmental Testing and Analysis →
Determines whether the product’s operational environment may contribute to failure.
Identification of residual species, primarily by ion chromatography analysis.
Identifies ionic and organic residues that may impact product performance, reliability and/or compliance to specifications.
Used to determine the root cause of failures, which is then used to find the source and mitigate the issue.
Provides a meaningful and accurate measure of the RoHS compliancy of a product.
Various industry standard inspections including IPC 610, Acceptability of Electronic Assemblies.
Identifies any product weaknesses or areas for improvement utilizing various, appropriate imaging techniques including SEM/EDS.
Metallurgical analysis allowing in-depth analysis of grain structures, including, for example, the inner layers of chips at up to 1000x magnification.
Characterizes organic and inorganic substances that could have a negative impact on your product.
Physical testing of such product aspects as solder joint strength to quantify improvements or compare methods.
Have questions about working with Foresite? Review our Standard Project Information or contact us.
It didn’t make sense.
They did everything right. They followed protocol. But their brand new product wasn’t delivering. Its batteries were draining while sitting on a shelf, waiting for shipment. They couldn’t figure out why it wouldn’t retain charge.
So they called Foresite.
We developed a high humidity screening test to separate the good units from the bad until we could figure out the root cause of the failures. We originally thought that the capacitors were cracked; however, multiple cross sectioning tests proved this idea wrong. Cleanliness wasn’t the problem. So we tried testing with a localized extraction system in the area of the capacitor on the failing units. We found a high level of sulfate residue on the capacitors. It turned out that otherwise perfectly functioning product had dirty 0805 chip capacitors on the battery circuit that were causing the three-volt battery to drain in less than two weeks.
Thanks to this tenacious habit of digging to find the root problem, our customer's electronics have retained their charge ever since.
Would you like to read about how Foresite solved this and other reliability challenges? Check out our case studies.