The Hidden Contamination Risks:
Brush Cleaning in No Clean Rework
In the world of electronic assembly rework, ensuring the reliability of products depends on stringent cleaning processes. However, a common yet underestimated practice—brush cleaning—can introduce significant risks if not properly managed.
This case study highlights how contamination from brushes used in rework processes impacts assembly reliability and explores actionable strategies to mitigate these risks.
The Role of Brushes in No Clean Rework
Brush cleaning, often performed with isopropyl alcohol (IPA), is widely used to remove flux residues following rework. Operators rely on this method to dissolve and visually clear residues, assuming it restores cleanliness. However, used brushes frequently become a source of contamination, spreading ionic residues across assemblies rather than eliminating them.
Case Study #3: Assessing Brush Cleanliness
A recent investigation of six assemblies examined the contamination levels of brushes used in a production environment over time. The goal was to determine how communal brush usage contributed to residue transfer and assembly reliability challenges.
Brushes from rework stations were collected after one month of use and analyzed using ion chromatography to measure levels of ionic contamination. The focus was on residues such as chloride, bromide, and ammonium. New, unused brushes served as a control group to highlight how contamination accumulates over time.
The results revealed significant contamination in the used brushes, including high levels of chloride and ammonium residues. Over time, brushes absorbed flux residues and retained ionic contaminants, which were subsequently redeposited onto assemblies during cleaning. In contrast, new brushes showed minimal contamination, confirming that residue accumulation occurred through repeated use. This finding underscores a critical oversight: while brushes may appear clean, their ability to absorb and redeposit contaminants poses a serious risk to assembly reliability.

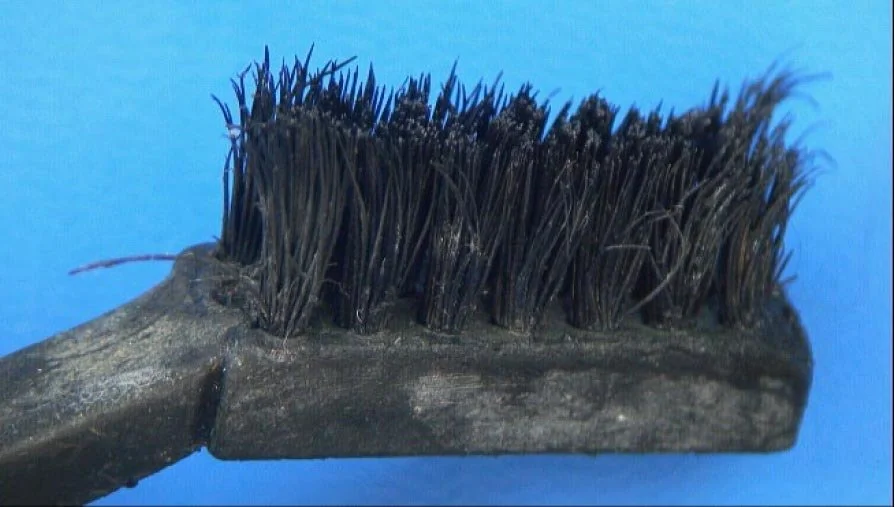
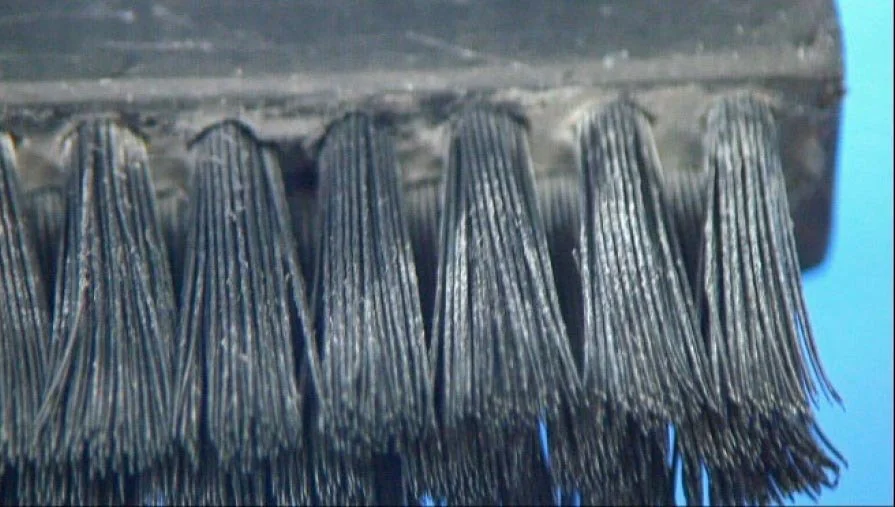
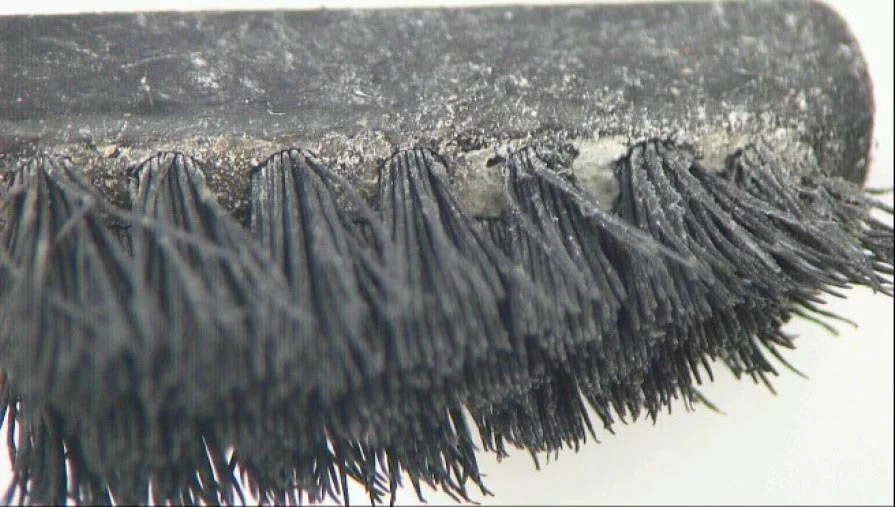
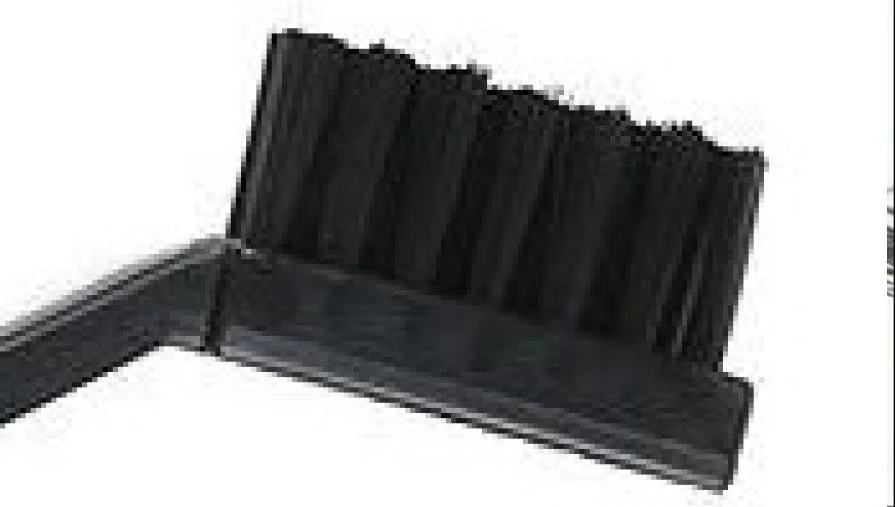
Reliability Implications
Contaminated brushes spread dissolved residues across circuits, increasing the likelihood of parasitic leakage, dendrite formation, and corrosion. Assemblies cleaned with used brushes exhibited reduced Surface Insulation Resistance (SIR) values, directly impacting their long-term reliability. This study highlights the importance of recognizing that even cleaning tools can become contamination vectors if not properly monitored and maintained.
[picture of charts]
Mitigating Risks in Rework Processes
To address the risks associated with brush cleaning, manufacturers should prioritize better management practices. Regularly replacing brushes is essential to minimize contamination risks. Controlled cleaning protocols, coupled with operator training, can also reduce over-reliance on brushes and ensure consistent cleaning techniques.
Adopting post-heating methods is a particularly effective alternative. Instead of using IPA and brushes, controlled thermal treatment can stabilize flux residues. This method transitions residues into a non-conductive state, enhancing electrical performance and reducing contamination risks.
Finally, periodic cleanliness assessments using ion chromatography or similar methods can help identify contamination sources and ensure that cleaning tools and assembly areas remain clean. These practices, when implemented together, significantly improve reliability and field performance.
Conclusion
Case Study #3 reveals a critical gap in traditional rework cleaning practices. Brushes, often treated as a reliable tool, can inadvertently compromise assembly reliability through residue transfer. By recognizing these risks and adopting best practices such as regular brush replacement and post-heating, manufacturers can ensure cleaner assemblies and improved field performance.
As the complexity of electronic assemblies continues to grow, eliminating hidden contamination sources becomes more vital than ever. By embracing clean processes and innovative solutions, the industry can confidently meet the demands of high-reliability applications.
For more information or to discuss tailored solutions for improving your rework processes, contact Terry Munson.